.jpg)
Improving Hospital HVAC Operations with Chiller Plant Optimization
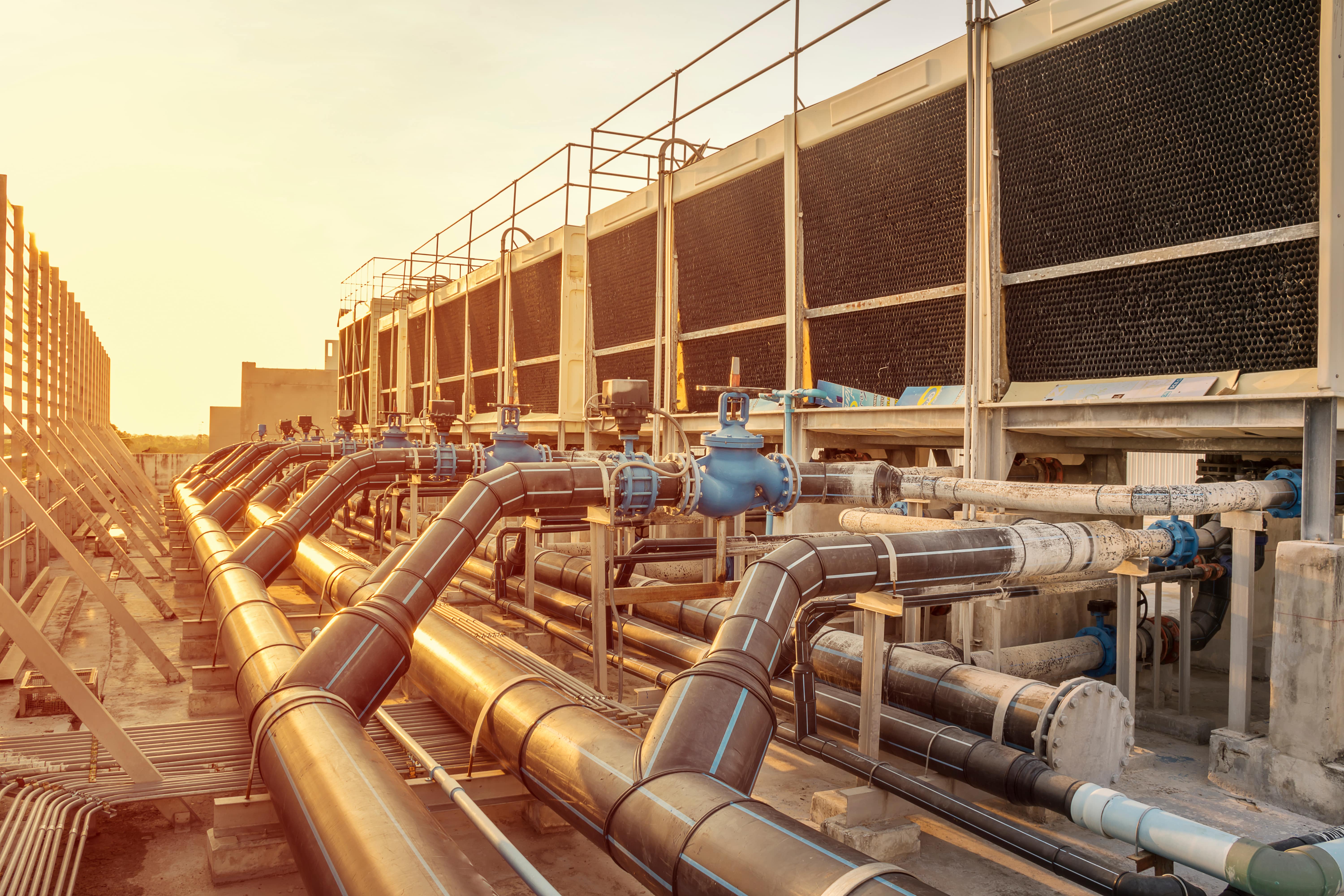
A hospital’s HVAC system shoulders most of the blame for its energy operating costs and greenhouse gas (GHG) emissions. Heating, ventilation, and space cooling accounts for 52% of hospital energy consumption.
Commercial cooling systems in particular are often tremendously inefficient. U.S. hospital cooling consumes 23.15 billion kWh of electricity per year. That’s the emissions equivalent of the entire city of Winnipeg.
Improving HVAC operations saves hospitals on both operating costs and building emissions. However, optimization is extraordinarily difficult. Hospital facilities have a continuous energy usage pattern, and must maintain comfort and safety despite constantly-changing demands on the system.
For most hospitals, chiller plants are the largest consumers of energy. Let’s examine four ways to improve chiller plant efficiency and reduce operational costs.
1) Chilled Water Reset
Under normal conditions, a hospital chiller system is designed to produce chilled water at a certain temperature, typically around 44-45°F (6.7-7.2°C). This temperature is chosen to ensure that the system can meet its maximum cooling load on the hottest days of the year.
However, on cooler days or times when the cooling load is less, maintaining this temperature might be more than what's actually required, leading to unnecessary energy consumption.
Chilled water reset adjusts the temperature of the chilled water based on the cooling demand or outdoor air temperature. For instance, if the outside air is cooler, or the hospital is not fully occupied, the control system could increase the temperature of the chilled water slightly, as not as much cooling is needed. This reduces the amount of work the chiller has to do, saving energy.
Hospitals can use machine learning software to automate their chilled water reset strategy. AI can learn from the behavior of the chilled water system over time, analyzing historical data on air temperatures and occupancy to predict future demand. By processing data from various sensors in real-time (like temperature, pressure, humidity, flow rates, and energy consumption), it can optimize the chilled water reset schedule, improving the energy efficiency of the entire system.
These controls can be automated as well. With the use of AI to continually monitor and analyze data to maintain optimal conditions, chilled water reset can be optimized without the need for human intervention. This can significantly improve operational efficiency and result in considerable energy and cost savings.
2) Condenser Loop Optimization
In a typical hospital’s HVAC system, the condenser loop releases the heat absorbed from the conditioned space into the external environment. The common practice for controlling these HVAC systems is fixed setpoint, which doesn’t take into account external factors like occupancy or weather conditions. This means opportunities to reduce energy consumption are regularly missed.
Beacon improves hospital HVAC efficiency to capitalize on these otherwise missed opportunities. It dynamically changes setpoint controls in response to utility rates, weather conditions, and how each component of the condenser loop is performing in real-time. Then it uses this information to alter setpoints affecting cooling tower fan speed vs. load size, flow rates of condenser water, and pump usage. These optimization recommendations are delivered automatically and continuously. Savings accrue without any operator involvement.
Hospitals with water-cooled systems can reduce their overall HVAC energy consumption by as much as 30% by deploying Beacon, with equivalent reductions in greenhouse gas emissions. Here is how a New York City hospital is using Beacon to reduce its operating costs.
Download our latest white paper to learn how to solve the problem of excess energy costs and emissions stemming from your hospital’s cooling system. Sections include:
- Introduction
- Do Less Harm: Healthcare’s Impact on Our Climate
- Green Legislation: The Cost of Inaction
- How Energy Efficiency Can Boost the Bottom Line
- Cooling Problem, Cooling Solution
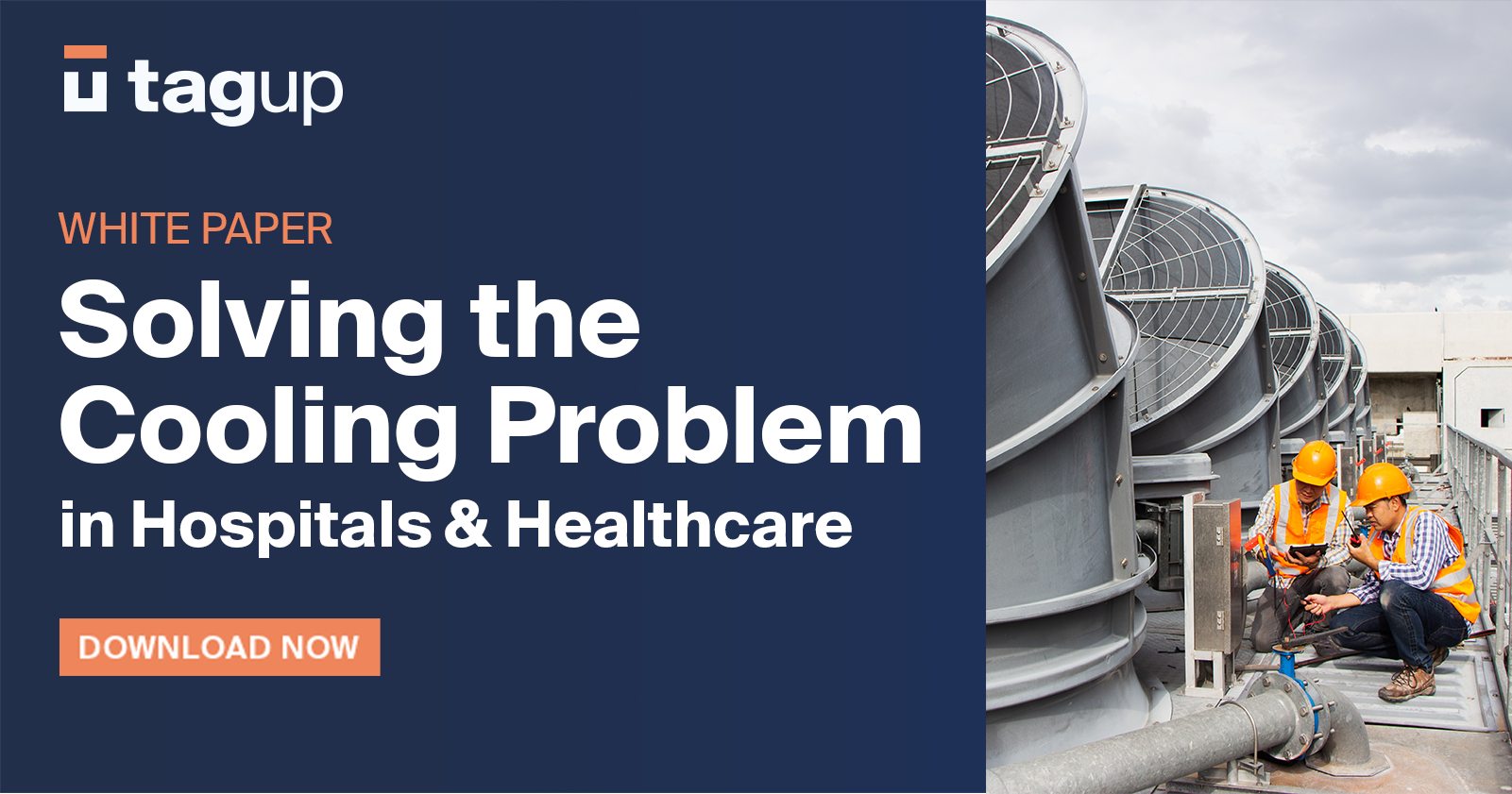
3) Chiller Staging
Chiller staging is the process of coordinating the operation of multiple chillers in a system to provide the required cooling load efficiently. When all the chillers are not required to run simultaneously to meet the load, some chillers can be turned off, which saves energy. Conversely, if the load increases, more chillers can be brought online.
The staging sequence, or the order in which chillers are brought online or taken offline, can have a big impact on a hospital’s energy consumption. The most common method for operating chillers efficiently is lead-lag, where one chiller runs constantly at near capacity, and “lag” chillers are brought online or offline as needed to meet the load. But, this can also lead to risks due to uneven wear and tear on equipment requiring increased maintenance, inadequate redundancy, and reduced energy efficiency if the load is less than full capacity of the lead chiller.
With advancements in AI, hospitals can now leverage machine learning technology to stage chillers for optimal energy efficiency and minimal waste. AI algorithms can analyze data from chillers and auxiliary equipment to optimize their operation for maximum energy efficiency. For example, AI can determine the optimal number of chillers to run at any given time, considering factors like the outside temperature, the load, and the efficiency curve of each chiller. These optimizations include real-time adjustments as well as demand forecasting based on historical data.
4) Predictive Maintenance
With HVAC equipment costs ranging from tens of thousands to millions of dollars, it’s critical for hospital operators to limit maintenance and replacement expenses. Foresight, Tagup’s predictive analytics software powered by machine learning, helps to do just that.
Integrating Foresight into your hospital’s building automation system provides visibility into HVAC event probabilities (drift, failure modes, excess load), forecasts time to specific events (failures, maintenance needs, etc.), and uses value modeling to turn predictions into economical, actionable recommendations. These insights allow operators to address issues before they become crises, saving on lifetime equipment costs.
Researchers have confirmed that HVAC predictive maintenance can diminish the cost of maintenance by a rate ranging from 25% to 35%, defeat breakdowns by a rate of 70% to 75%, and decrease the time of breakdowns with a rate of 35% to 45%. Contact us for more information about Foresight for predictive maintenance.
Turnkey Deployment
Tagup has developed our own hardware that can be installed on a hospital’s building management system in minutes. Our industrial PC simply requires access to a power outlet, ethernet port, and network access.
Once the hardware is installed, Tagup starts generating savings within weeks. Current deployments are yielding an average 10-20% savings on costs and emissions, with peak savings up to 30%.